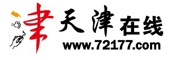
首页 > 资讯中心 天津
天津七所高科转型 依靠自主创新成为行业领头羊
2015年02月24日 20:32天津日报记者 张璐 焊接是汽车行业的基础技术,一部汽车的成型和稳定性取决于材料和焊接工艺的有机结合。从低级的手动焊接设备到高端的机器人柔性工作站,天津七所高科技有限公司依靠自主创新,成功实现了产品的转型升级和企业的结构调整。目前,天津七所高科的机器人柔性工作站等产品已在上海大众、东风本田、神龙汽车等全国400余家汽车整车厂及配件厂中广泛使用,是汽车行业更新换代、替代进口的主导产品,占据国内市场半壁江山,成为该领域国内第一大品牌,综合实力全国第一,并出口到俄罗斯、乌克兰等多个国家。
记者走进坐落在北辰科技园的天津七所高科的生产车间,研发人员正在调试刚组装完的一台机器人柔性工作站。这个看似笨重的家伙,正伸出螃蟹钳子一样的铁手臂,上下翻飞,根据焊接零件的型号,自动选择焊枪,然后快速而又准确地焊接。据介绍,这个智能机器人柔性工作站系统融合了多项国家发明专利和实用新型专利,大幅度提高了国内焊机的焊接稳定性和国内汽车行业焊装水平。和传统焊机相比,它的效率提高50%,人工也节省50%,代表了我国汽车自动化焊接装备的最高水平。
天津七所高科副总工程师张海勇告诉记者,这款机器人工作站可以通过一套设备里不同的程序,同时自动焊接4到5种不同的零件,在工作性能上更加柔性化和智能化。
随着汽车行业不断的发展,传统的焊机已经不能满足焊接的需求。尤其是2007年和2008年,国内汽车行业普遍不景气,传统的手动焊接设备订单减少,汽车企业对设备的自动化水平要求越来越高,产品如果不能及时升级换代就会被市场无情地淘汰。2009年天津七所高科果断将还处在研发阶段的机器人柔性工作站项目加紧进行产业化,2010年首套设备成功应用于江苏华达汽车零部件公司,由此开启了国产机器人柔性工作站市场化的大门。2013年,传统手动焊机产品市场需求大幅下降,天津七所高科订单从2010年的4500套减少到3000套,销售收入也由1亿元下降到6500万元;与此同时,机器人柔性工作站系统逆势上扬,订单从2010年的仅仅1套增加到30套,销售收入也由100万元上涨到4500万元。
如今,天津七所高科已经形成了悬挂式点焊机、新型工频及逆变一体化悬挂式焊机、固定式点焊机、焊机集中控制联网管理系统、机器人点焊钳和电阻焊专机等六大梯队产品。系列产品共申请35项国家专利,起草3项国家标准、1项机械行业标准,其中1项是国家强制标准。公司总经理戴永康骄傲地说:“现在只要是在中国销售的焊接设备,就必须通过我们制定的安全认证。未来我们的产品还将不断升级,争取集站为线,提供汽车柔性焊装生产线,实现真正的汽车柔性生产,打破国外公司的垄断。”
通过转型升级,天津七所高科增强了核心竞争力,提高了发展质量,并且带动了我国汽车领域高端装备制造业的发展。据了解,自去年2月8日,全市召开“促惠上”活动暨万企转型升级行动动员大会以来,天津涌现出一批可复制、可推广、可借鉴的典型经验和成功案例,形成了较好的示范效应,有效引领带动了一批企业和载体全面快速提升。
去年,天津围绕技术改造、专精特新、专利引领、管理提升、战略新兴产业转型、现代服务业转型、培育电商、关停淘汰、兼并重组、园区转型升级、楼宇全面提升等十一条路径,全面开展帮扶活动。成立了30个市级“促惠上”服务组和11个转型升级帮扶组,筛选了300家经济效益较高、市场前景较好、发展潜力较大的企业,列入市级重点帮扶对象;16个区县共筛选确定717家重点帮扶企业,为企业讲政策、送服务、解难题、促转型。分类指导、综合施策,集中抓好示范带动作用强的优质企业,淘汰关停污染严重的落后企业,推动发展势头好的潜力企业,有力地推动了万企转型升级行动的全面实施。
责任编辑:wb001
文章来源:http://news.72177.com/2015/0224/1929009.shtml